Blog
Decoding The Complexity of Granite Manufacturing
In recent years, granite has superseded marble as one of the most widely preferred natural stones in the realms of architecture and construction. It is not just the untamed beauty of granite stone that makes it a hot choice among architects, there are some charismatic characteristics of granite that give it an upper hand over other natural stones. Despite being a natural stone, the role of manufacturing and technology is quite high in its processing. Be it is the surface finish of the stone or cutting the stone in precise measurements, technology plays an indispensable role when it comes to getting that perfect stone finish and size.
India is home to numerous granite manufacturers that make use of advanced machinery and technology to prepare the finest quality granite products. As a granite importer or dealer, it is necessary for you to have the knowledge of granite manufacturing, machinery used, and its importance.
Let’s get to know more about granite manufacturing in the latter part of this post.

What is granite?
Granite is an intrusive igneous rock comprised of feldspar and quartz. It forms from beneath the Earth under intense heat and pressure. This is known as intrusive granite, one of the two granite classes that indicates the usual site of granite. The intrusive granite that we know is formed by the cooling and solidification of magma below the Earth’s surface. Conversely, granite that cools on Earth’s surface is known as extrusive granite. Volcanic eruptions are usually responsible for their ejection onto the Earth’s surface. They are brittle and flaky because of their low cooling periods brought on by atmospheric exposure.
Essentially, there are four stages of granite formation such as:
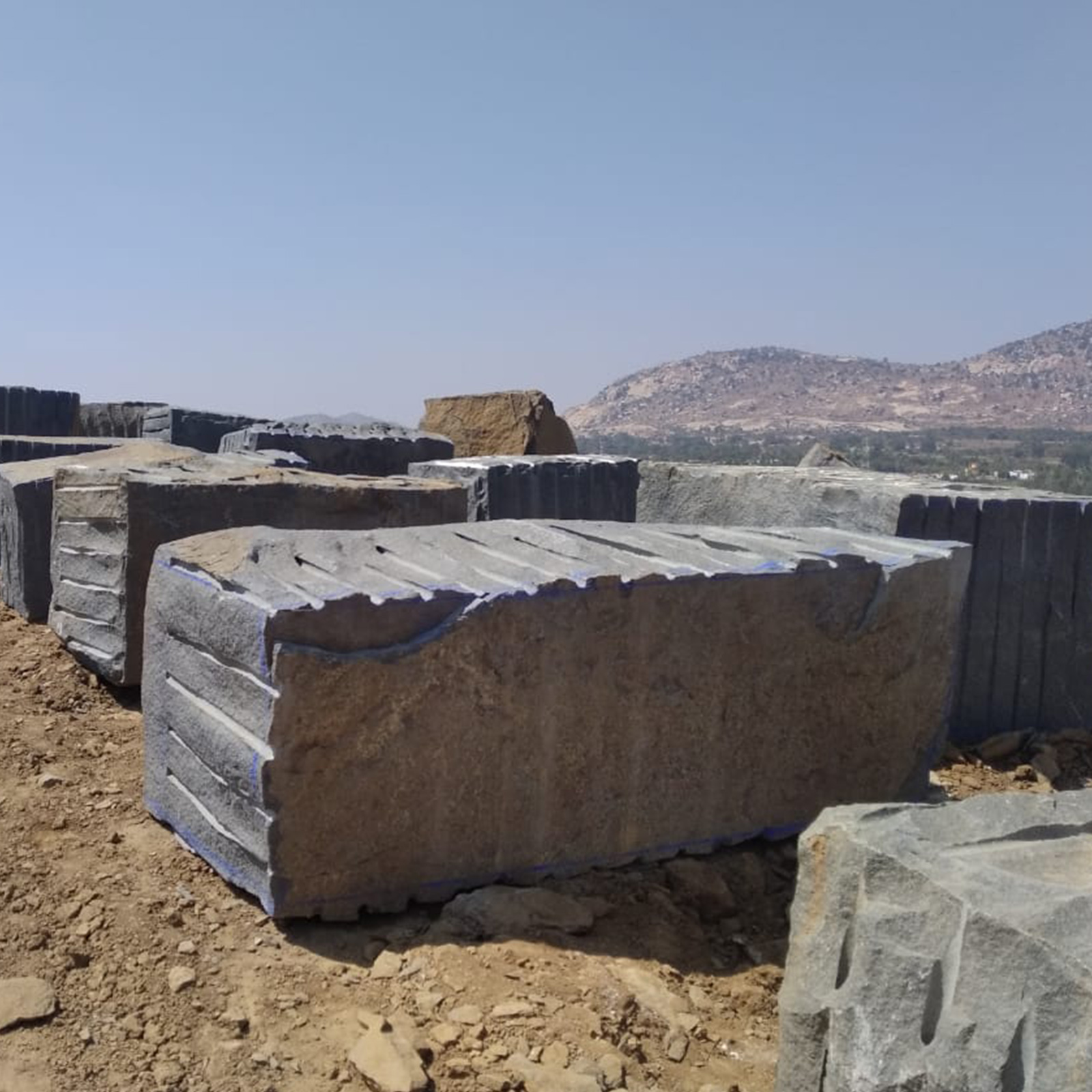
Magma Formation: Granite originates from molten rock, known as magma, which forms deep beneath the Earth’s surface. This magma can be produced when rocks melt due to high temperatures, pressure changes, or the addition of fluids.
Cooling: The magma slowly cools and solidifies underground. The slow cooling process is crucial as it allows large crystals to form. The longer it takes for the magma to cool, the larger the crystals can grow.
Crystallization: As the magma cools, different minerals crystallize at different temperatures. Common minerals in granite include quartz, feldspar, and mica. These minerals interlock like a jigsaw puzzle, giving granite its coarse-grained texture.
Emplacement: Eventually, the granite may be exposed at the surface through the process of uplift and erosion of the overlying rock.
Different Stages of Granite Manufacturing
Though granite is a natural stone, its manufacturing takes place in several stages, as there are different types of treatment done on granite before it is used in an application. From the initial extraction of granite blocks from quarries to final delivery, specialized machines are used at every stage to deliver the final product. Let’s look at the details and machinery used at every stage.
Quarrying
Granite comes from quarries that are primarily located in the Southern part of the country. There are several granite quarries in India that produce the finest quality granite stones. Wire saws are used to cut the blocks, and JCBs are used to handle them without causing damage. This is the first stage in granite manufacturing.
Machinery used
Diamond Wire Saw – This saw uses a wire embedded with diamond sections to cut the granite blocks from the quarries. It is the most commonly preferred way of extracting granite blocks from a granite quarry.
Drilling Machine – Drilling machines are used by quarry owners to make holes for inserting diamond wire, which helps break the granite blocks from the bedrock.


Cutting
The next involves the transportation of granite blocks to granite processing units, where they are cut into gangsaw/cutter slabs or tiles. This is often done using gang saws and bridge cutters, which are large machines equipped with multiple blades to slice through the granite simultaneously. More precise or complex cuts may be achieved with water jet cutting, which uses high-pressure water mixed with an abrasive.
Machinery Used
Gang Saw – A gang saw is used to cut granite gangsaw slabs from a granite block. This is a large cutting machine used in the granite industry.
Multi-Cutter – As its name indicates, this cutting machine contains multiple blades of different diameters that work in tandem to cut several granite slabs from a block.
Bridge Cutter – A bridge cutter machine is typically used to do more precise cuts, given the specific dimensions. However, it is used to cut smaller or custom-sized granite slabs.
Polishing
Once the cutting is done, polishing is done on granite to highlight its natural color and pattern. Different types of abrasive materials are used to polish the stone surface. In most cases, automatic polishing machines are used to do the polishing job. This procedure also seals the pores on the granite surface, which makes the stone more resistant to stains.
Machinery Used
Automatic Polishing Machine – This is a conveyor-based machine equipped with polishing heads that treat the granite slabs as they pass through, resulting in a uniformly polished surface.


Finishing
Additional finishing touches might include edging and quality inspection. Edging involves shaping the edges of the granite slabs or tiles to specific profiles, such as rounded, beveled, or squared. Each piece is also inspected for defects and quality before it leaves the factory.
Machinery Used
Edge Profiling Machine – This machine is used to shape the edges of granite into different profiles like bullnose, bevel, or ogee, which are commonly seen on countertops.
Delivery
Once the granite is processed, the finished granite products are packed and shipped to suppliers or directly to construction sites where they will be installed as countertops, wall cladding, flooring, or other architectural elements.
Why choose Regatta Granites India?
Regatta Granites India has been manufacturing and exporting quality granite products worldwide. Some of its wide-ranging products include gangsaw slabs, cutter slabs, tiles, monuments, thresholds, window sills, treads, steps, countertops, and others.
Being in the sector for nearly 30 years, Regatta has gained an unparalleled edge over its competitors. The granite manufacturer in India has state-of-the-art machinery that includes multi-cutter machines, single blade block cutter, bridge cutting machines, edge cutting machines, automatic slab polishers, hand polishers, gantry crane, calibration machine, and others.
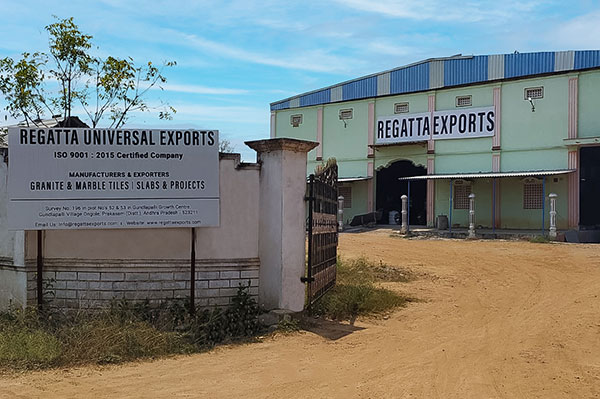