Blog
Things To Know About Granite Blocks
In recent times, granite has become one of the most commonly used construction materials in the world. And, it is not just a fad, but the natural stone is full of visual and physical qualities that make it super special in the eyes of architects and homeowners. Be it a residential construction project or a commercial one, the stone exhibits superb performance in all weather conditions from scorching heat to bitterly cold. In addition, the stone requires lesser maintenance as compared to its counterparts like marble.
What is granite?
Granite is an igneous rock which means it is formed by the cooling of magma that emerges from volcanoes. There are different elements present in the granite that define its structural composition and color.
When magma slowly cools inside massive, deeply buried rock masses known as plutons, numerous separate crystalline structures closely coalesce to produce granite’s distinctive grainy texture and strength. Plagioclase and alkali feldspars, of which the former may not exceed general equilibrium, and quartz make up 20–60% of true granite.
Granite may also contain other reserves, such as biotite and hornblende, which accounts for the range of looks. In the business world, the word “granite” refers to a variety of other dimension stone varieties, such as any feldspathic crystalline stones or other igneous or metamorphic stones that have characteristics like the granular, interlocking structure of granite.
Granite comes in a wide variety of varieties, with the most popular fundamental colors being white, grey, red, and pink. Darker colors including greens, browns, greys, and black can also be found in granite.
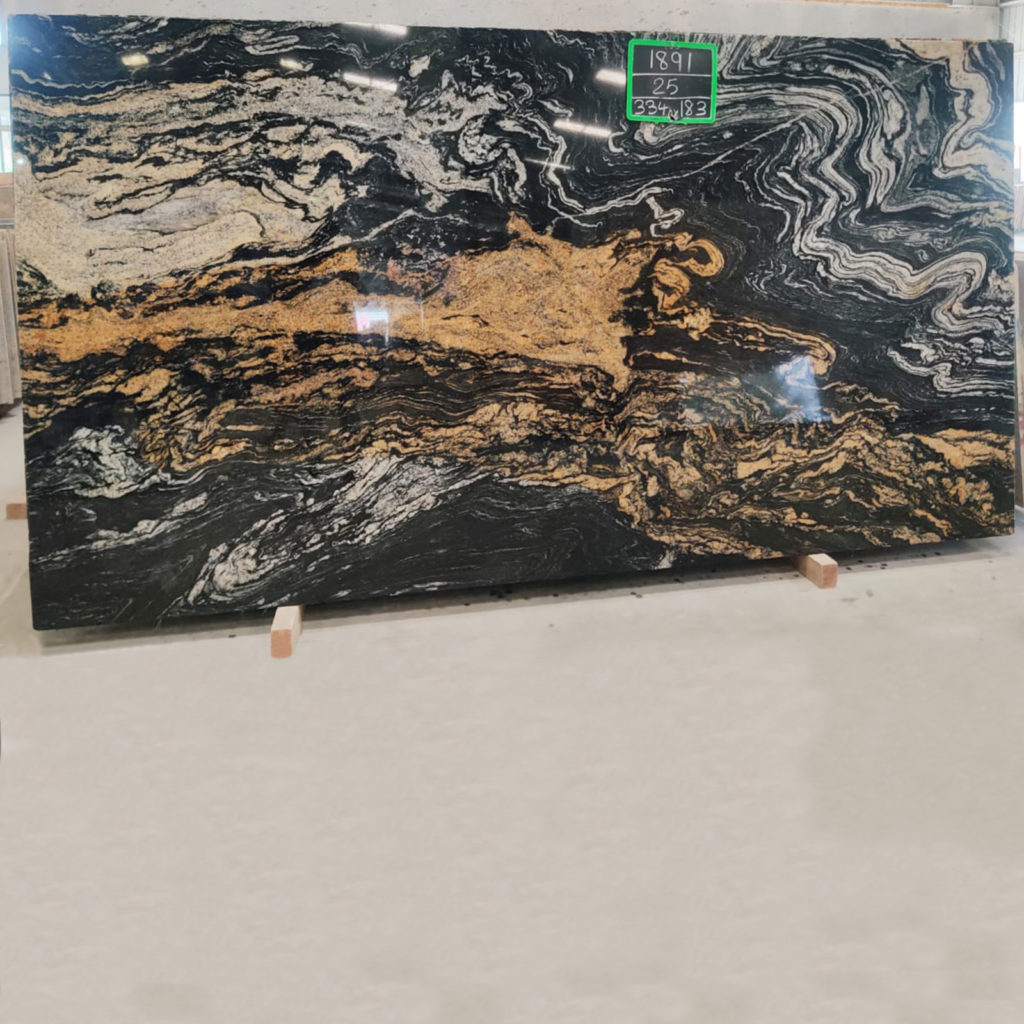
Let’s get to know how GRANITE BLOCKS are extracted and processed.
Extraction
The process of extraction, also called quarrying, refers to procuring stone blocks or individual pieces out of a discovered and defined geologic deposit. Differences in the physical characteristics of the pledge itself, such as density, depth, and fracturing/bedding planes, can lead to differences in the specific quarrying procedures that are employed.
Getting entree the granite deposit is the first stage in the quarrying process. This is accomplished by using heavy machinery to remove the layer of soil, grass, and rock that is inappropriate for the product and relocating it to on-site storage for prospective use in a later site reclamation. The granite is extracted from the quarry in bleachers, typically 8 to 12 feet square and going up to 20 feet or more, employing a range of processes according to the geology and properties of the granite reserve once the face of the granite has been exposed.
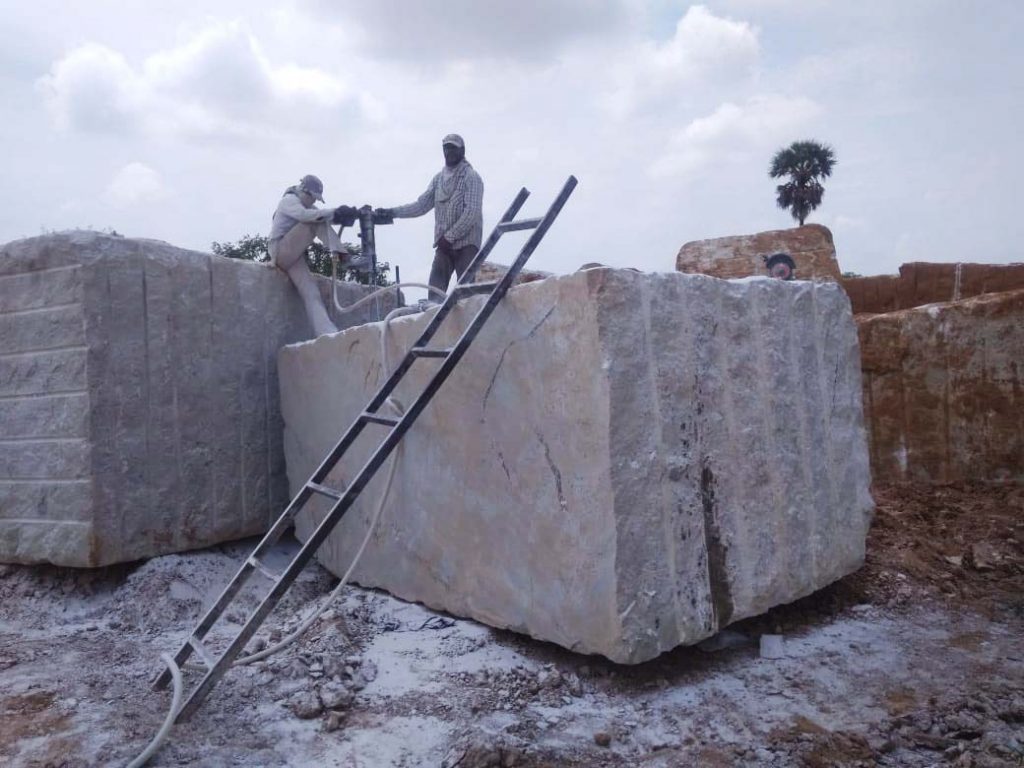
Getting entree the granite deposit is the first stage in the quarrying process. This is accomplished by using heavy machinery to remove the layer of soil, grass, and rock that is inappropriate for the product and relocating it to on-site storage for prospective use in a later site reclamation. The granite is extracted from the quarry in bleachers, typically 8 to 12 feet square and going up to 20 feet or more, employing a range of processes according to the geology and properties of the granite reserve once the face of the granite has been exposed.
In a quarrying operation, holes are often drilled around the bench’s edge, and then the stone is either split using hydraulic splitters or tiny explosive charges, or it is cut out of the deposit using diamond-wire-equipped saws. Heavy machinery is required to raise the granite bench after it has been cut or broken away from the deposit so that it can be checked for quality and size criteria.
Each block that satisfies the size requirement is then meticulously examined for quality requirements. Our staff, which includes the directors, has the most expertise. They visit the quarry and examine the blocks that will be processed further. The blocks are examined for fissures, fractures, color patterns, and other differences that aid in the selection of the best blocks for processing.
Cutting of Granite Blocks
Gangsaw
The first and foremost step of granite processing is to cut and shape the stone. In most cases, this process is done using a wire-saw cutter. During the operations of the machine, an incessant stream of water is used to release the heat produced during the process, thereby averting machine and material damage.
To prevent breaks or fractures during the cutting process, the matting is completed after the block has been formed with the wire saw. The gang-saw machine’s blades are adjusted to the rock’s hardness and the required thickness for cutting, taking into consideration any thickness loss during cutting and subsequent processing. To guarantee there is no movement throughout the cutting process, the granite block is put into the tray and filled with cement before being allowed to dry for a day.
After that, the gang-saw machine receives the tray containing the granite block. The gutting of the block is aided by the use of a slurry, which is a combination of water, lime, and grit that also serves to absorb any heat generated during the cutting process. Every material and the cutting process requires intense monitoring and adjusting of the slurry’s viscosity.
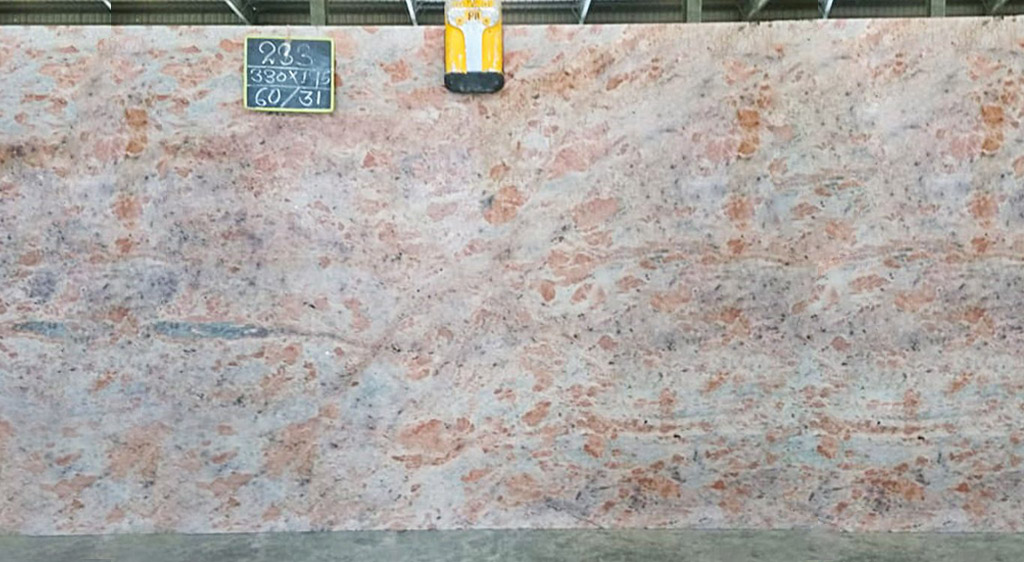
Cutting
The granite blocks are then transported to the cutting machine once it has been formed. The blades’ width is modified in accordance with specifications. There are many different types of cutter machines, ranging from those with just one blade to those with as many as ten. The process of cutting a block proceeds more quickly the more blades there are. Nonetheless, blocks of non-standard size or thickness are processed using single-blade cutter machines.
A stream of distilled water is additionally sprayed while the material is being cut in order to soak up any heat that escapes and reduce sparks. The blocks are chopped until just a few inches remain, at which point a group of stone experts cut and removed each slab off the block individually. Following a thorough inspection for any flaws, these slabs are given numbers for inventory monitoring and transferred for further processing.
A stream of distilled water is additionally sprayed while the material is being cut in order to soak up any heat that escapes and reduce sparks. The blocks are chopped until just a few inches remain, at which point a group of stone experts cut and removed each slab off the block individually. Following a thorough inspection for any flaws, these slabs are given numbers for inventory monitoring and transferred for further processing.
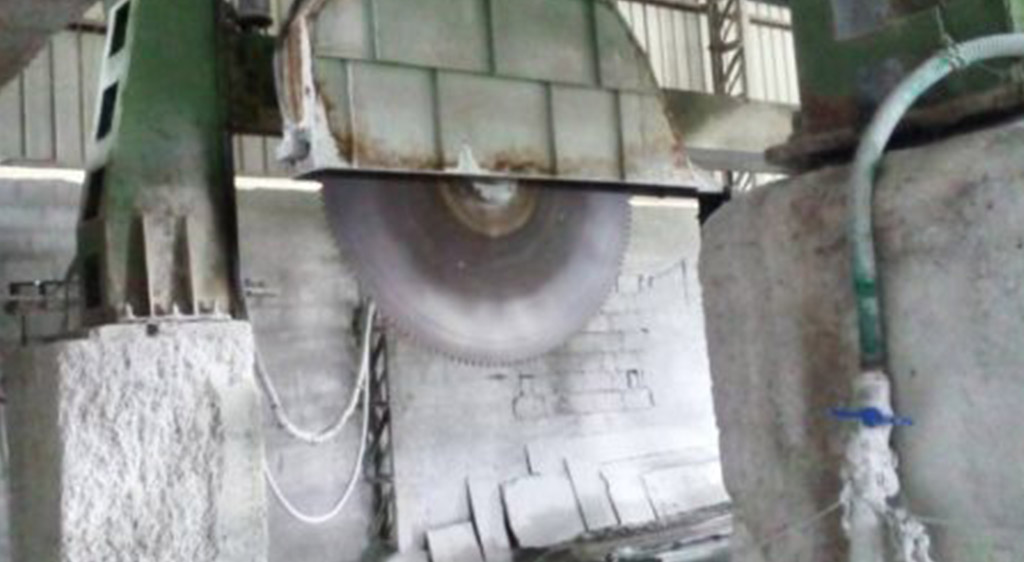
Grinding
The slabs are transported for grinding after being cut and labeled. The purpose of grinding is to remove the grainy finish that results from the cutting process from granite surfaces so that they are smooth to the touch.
To produce a consistent surface polish, grinding is done in a machine equipped with many heads that are connected to diamond abrasives of various densities. To reduce the amount of heat produced by friction, water is once again utilized in this process.
Epoxy Coating
To guarantee that the stone is further cemented, epoxy resin is used to cover all of the pits and micro-fissures that are present naturally. This procedure ensures that granite maintains its inherent beauty and matures properly over time. The granite’s inherent color and pattern will be brought out and highlighted when the epoxy it is coupled with is combined with the right granite hue.
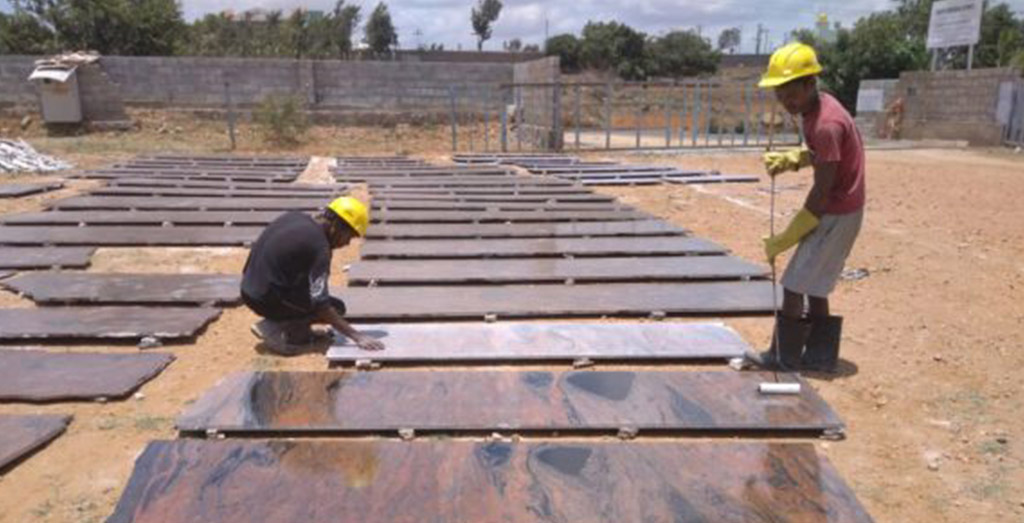
The surface of a granite slab must be heated prior to treatment in order to allow the rock to absorb the resin. In order for the resin to effectively penetrate even the smallest fissures on the surface, the material must be perfectly clean and dry. For the optimum finish, a variety of epoxy chemicals are matched with the appropriate color, and the application method is also crucial.
The entire surface is subsequently covered with resin, which is then warmed to enable deeper epoxy penetration. Following that, the epoxy further hardens the granite slab as it cools.